Learn 10 key safety tips for operating a man lift crane and keep your worksite safe from accidents.
Working at height always comes with risks, especially when using heavy equipment like man lift cranes. These machines are essential in modern construction, but only when they’re operated correctly and safely. Whether you’re trimming trees, fixing a roof, or building high-rises, safety should be your first concern.
1. Introduction
Man lift cranes—also known as aerial work platforms or cherry pickers—are designed to lift workers and their tools to elevated areas safely. But when handled carelessly, these machines can become dangerous. That’s why proper operation, routine inspection, and on-site awareness are so important.
In this post, we’ll explain how to:
- Ensure operator training
- Conduct pre-operation inspections
- Check ground stability
- Secure fall protection
- And more…
Each of these tips can make a big difference in how safe your team is while working at height. If you follow them carefully, you’ll not only meet safety rules but also protect your people, equipment, and deadlines.
2. Ensure Operator Training
Why Operator Training Matters
Would you let someone drive a truck without a license? Of course not. The same logic applies to man lift cranes. Only trained, licensed professionals should operate this type of equipment. That’s why Ensure operator training is our number one rule.
Without proper training, operators might:
- Misjudge platform height or range
- Fail to follow load guidelines
- Skip safety checks
- Forget how to respond to an emergency
This can lead to serious accidents—not just for the person in the lift, but for everyone on the ground too.
What Training Should Include
At Jugnoo Transport, we make sure our crane operators go through certified courses and regular refreshers. A solid training program should cover:
- How to operate each lift model
- Emergency shutdown procedures
- Fall protection basics
- Weather condition guidelines
- Site safety coordination
We also encourage clients to ask for operator credentials before renting any equipment. If you’re unsure, we’re happy to supply one of our certified, trained professionals as part of your package.
Refresher Courses and Upgrades
The construction industry keeps changing, and so do its safety standards. That’s why retraining is essential. An operator who was trained five years ago may not know the latest regulations or machine updates.
We offer in-house refresher sessions and keep all our operators updated with the latest safety knowledge. It’s all part of our promise to deliver not just equipment—but safety and peace of mind.
3. Conduct Pre-Operation Inspections
Don’t Skip the Checklist
Before you raise that lift, take a few minutes to check it. Why? Because even the best machines can wear down over time. A loose bolt, flat tire, or leaky hydraulic system could lead to disaster if not caught early. That’s why we strongly urge you to conduct pre-operation inspections—every single time.
What to Inspect
Here’s a basic checklist we use at Jugnoo Transport before any man lift goes out:
- Tires and wheels – Proper inflation, no cracks or wear
- Hydraulics – No leaks or strange noises during extension
- Platform and guardrails – Fully intact, no rust or damage
- Controls – Respond properly, no lag or overcorrection
- Safety switches – Emergency stop buttons must work
- Fall arrest attachment points – Secure and tested
If anything looks off—even a small leak—report it immediately. It’s better to delay a job than to risk injury.
Keep a Record
At Jugnoo Transport, every crane comes with a logbook. Our operators note down:
- Last inspection date
- Any issues found
- What maintenance was performed
This builds trust, improves safety, and meets regulatory compliance too.
By making pre-operation checks a habit, you’ll avoid unexpected downtime, save money on repairs, and—most importantly—keep everyone safe.
4. Check Ground Stability
A man lift is only as safe as the ground beneath it. Before moving or setting up the crane, always check ground stability. Soft or uneven terrain can cause tipping—even if the lift is parked carefully.
What to Look For
- Visible signs of weakness – mud, wet soil, or recently disturbed earth
- Cracks or subsidence – in pavement or concrete surfaces
- Water pooling – can sink the wheels during operation
- Incline or slope – even small changes can affect stability
At Jugnoo Transport, we evaluate every worksite and use support pads or plates when needed. In soft soil, we may also use timber or steel outrigger mats to spread the load and increase stability.
Why This Tip Matters
- Prevents the risk of the lift tipping over
- Ensures that all levels of the lift operate smoothly
- Keep personnel around the lift safe from sudden shifts
This step may take a few minutes—but it protects your team and avoids costly accidents.
5. Use Secure Fall Protection
Working off the ground demands respect for safety. That’s why it’s essential to always use secure fall protection when using a man lift crane.
Must-Have Safety Gear
- Harness with lanyard – to keep you attached to the platform
- Guardrails – check for gaps or loose fittings
- Anchor points – secure and properly rated
- Toe boards – keep tools from falling off
Jugnoo Transport only provides cranes that meet fall protection standards. We supply high-quality harnesses, educate operators on correct fitting, and insist that protective gear is worn before the lift starts. Also, we make sure no one can loosen or bypass these safety features and that they are secure fall protection systems truly effective at height.
Ensuring Compliance
- Inspect the harness condition and expiry
- Train operators in attachment techniques
- Regularly check anchor points for solid attachment
- Enforce continuous gear use during operation
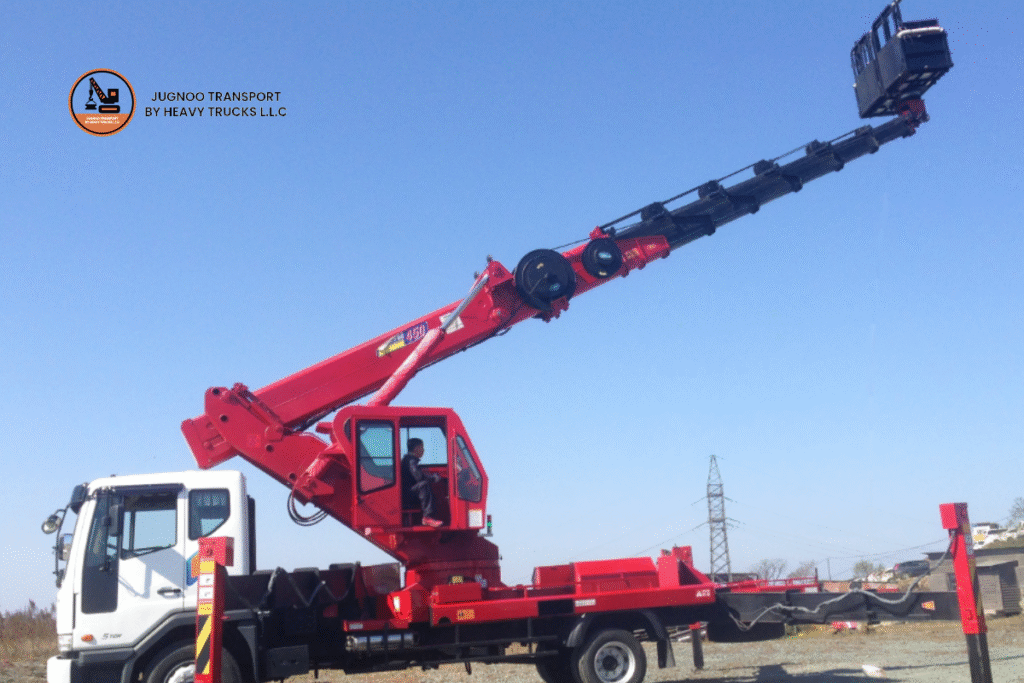
6. Plan for Overhead Hazards
Before raising a man lift (or moving it into position), you must conduct a site survey to watch out for overhead hazards.
Things to Watch For
- Power lines – Even being near one can cause electrocution
- Tree branches – Risk of dislodging and injury
- Building overhangs or signs – Can block operations or damage equipment
- Scaffold poles – Risk of hitting or snagging
Mitigation Strategies
At Jugnoo Transport, we always:
- Use a spotter to assist the operator
- Establish exclusion zones where no one is allowed beneath the lift
- Plan the best approach path free of hazards
- Halt work and reposition if conditions change or hazards appear
Our operator training programs stress the importance of recognizing and avoiding overhead risks. By doing this, you help protect both the machine and your team from accidents.
7. Monitor Weather Conditions
Before and during use, keep an eye on weather. Strong winds, rain, and storms can make operating a man lift very dangerous. That’s why we always monitor weather conditions as a key safety step.
What to Check
- Wind speed – High gusts can cause swaying
- Rain – Makes surfaces slippery and controls harder to use
- Lightning or storms – Stop immediately in severe weather
At Jugnoo Transport, we use weather apps to check forecasts before every job. If wind exceeds safe limits—usually above 28–32 km/h—we delay or cancel the lift. Rain prompts us to secure the equipment and reschedule for dryer conditions.
By proactively tracking weather, you protect both crew and equipment without risking accidents.
8. Follow Load & Span Limits
Every man lift crane has specific load and span limits—how much weight the platform can hold and how far it can safely reach. Exceeding these limits is dangerous, so always follow load & span limits.
What You Should Do
- Read the load chart before use
- Include people and tools in the weight total
- Never overreach the boom arm
- Follow the manufacturer’s safe-use guide
Jugnoo Transport provides clear documentation with each lift so operators know exactly how much the platform can safely carry. Strictly staying within these limits avoids tip-overs or mechanical failure.
9. Emergency Preparedness
Even with the best plans, emergencies happen. That’s why every lift team needs to be ready, with a solid emergency preparedness plan.
Key Components
- Emergency lowering controls – Accessible buttons to safely lower the platform
- Communication systems – Radios or phones to call for help
- Rescue plan – Steps to retrieve someone if the lift fails
- Operator drills – Regular practice of emergency scenarios
At Jugnoo Transport, our operators train in emergency response, and each site includes clear rescue plans. We teach how to use emergency stops and lowering procedures and ensure someone on site can activate them instantly if needed.
10. Maintain Equipment Regularly
Routine Maintenance Saves Lives
A well-maintained lift is a safe one. Skipping maintenance might lead to mechanical failures at the worst moments. That’s why you must conduct regular maintenance as part of your safety routine.
Where to Focus
- Check hydraulic systems – regularly inspect hoses, valves, and fluid
- Test electrical systems – controls, alarms, and lights
- Lubricate joints and bearings – to reduce wear
- Inspect wheels and brakes – ensure proper stopping power
At Jugnoo Transport, every man lift crane goes through a professional check every 50–100 hours of use. We keep logs so you can see exactly when maintenance was done, ensuring reliable, problem-free operations.
Conclusion
Safe man lift crane operation isn’t just a checklist—it’s a way of working. By focusing on these top 10 safety tips:
- Ensure operator training
- Conduct pre-operation inspections
- Check ground stability
- Use secure fall protection
- Plan for overhead hazards
- Clear the work area carefully
- Monitor weather conditions
- Follow load limits
- Emergency preparedness
- Maintain your equipment
you build a work environment that values safety and professionalism.
At Jugnoo Transport, safety isn’t optional. Whether you’re renting a crane or buying time and training, we’re here to support your safe success—every time.
FAQs
You should ensure operator training that covers machine operation, emergency stops, fall protection use, and handling weights. Licensed professionals have completed certified courses and ongoing refreshers.
Before every shift or job. Even small issues can become big problems when working at height.
Unstable ground increases tipping risk. Checking for firmness and using support pads or mats ensures safe operation.
Wear harnesses, lanyards, and secure anchor points to prevent serious injury or death in the event of a fall.
Follow the rescue plan, use emergency lowering controls, and maintain communication with site teams. Regular drills ensure everyone knows how to act.